CASE STUDY
Japan Railway H station
- Rotary Blade Type Bag Breaker & Separator
- Food related
Sanyu’s Bag-Breaker and Separator is used to separate and dispose of food waste generated by commercial facilities in H station.
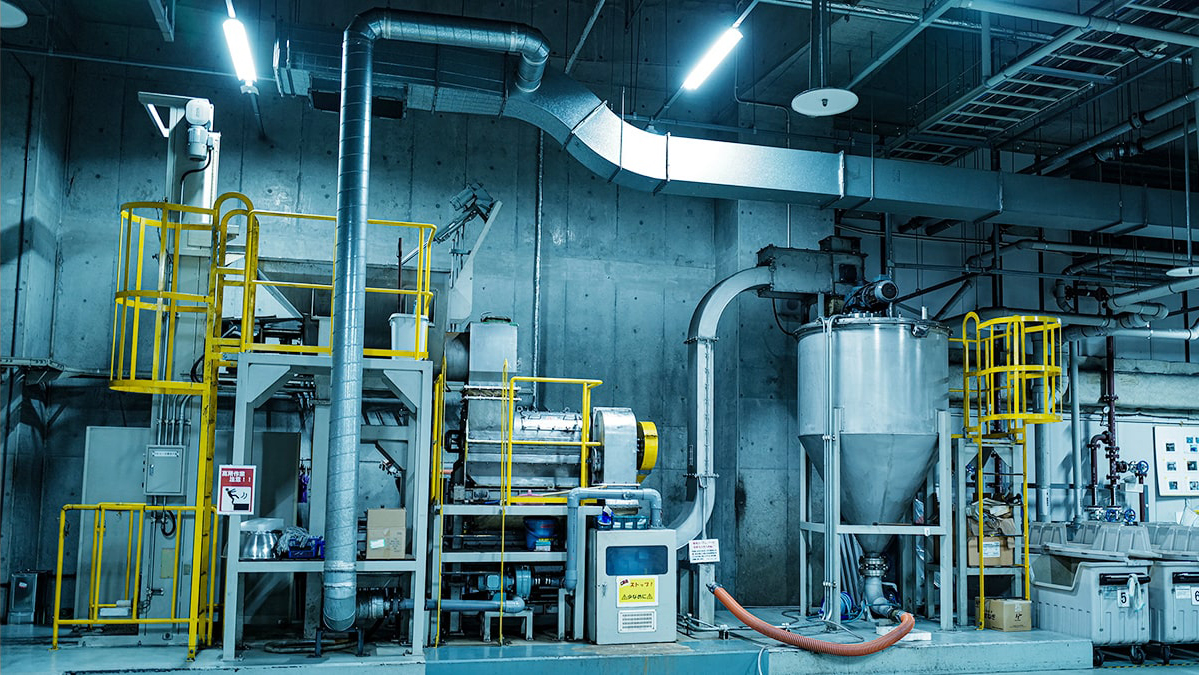
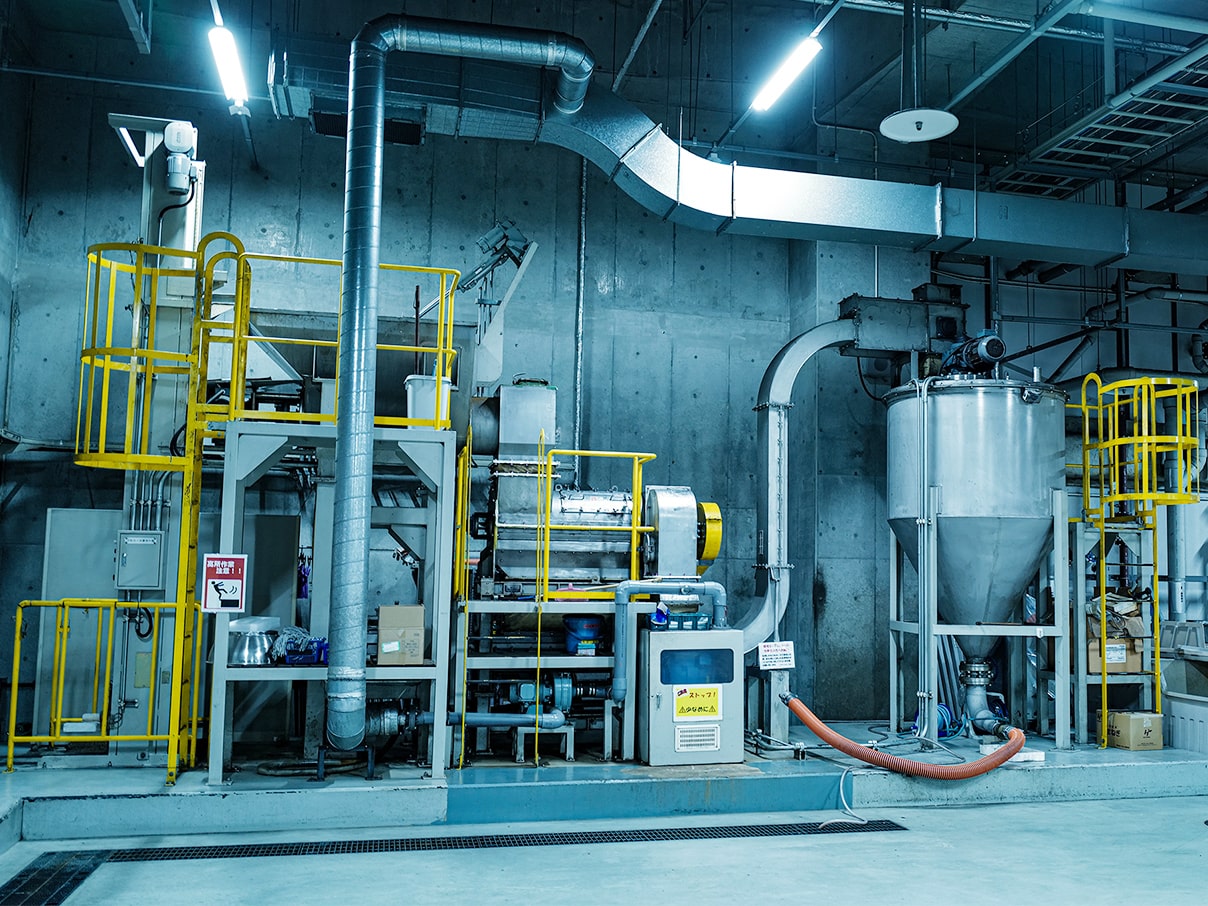
Place of installation
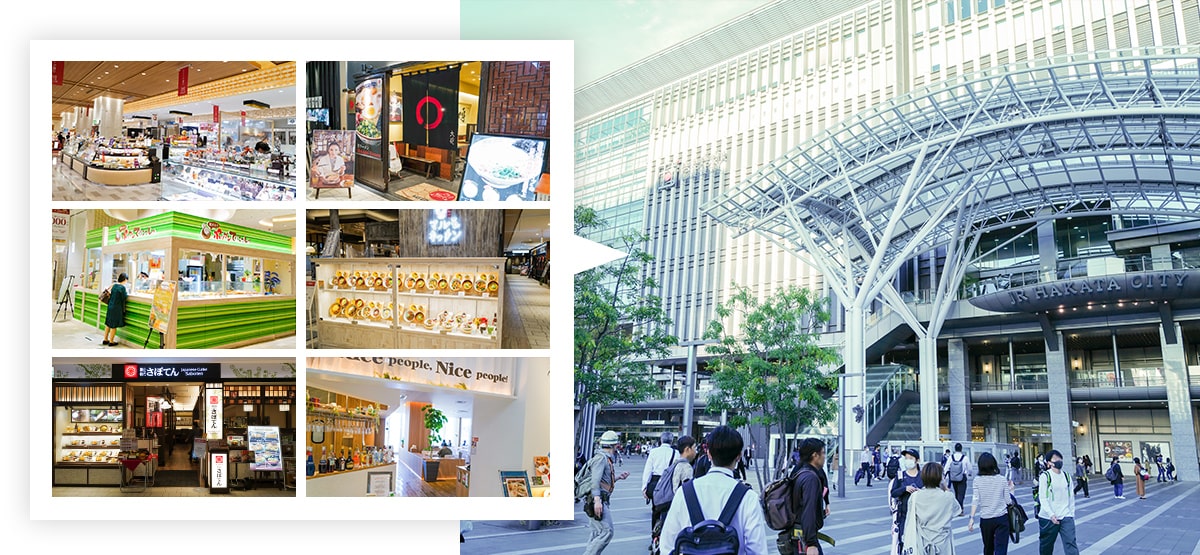
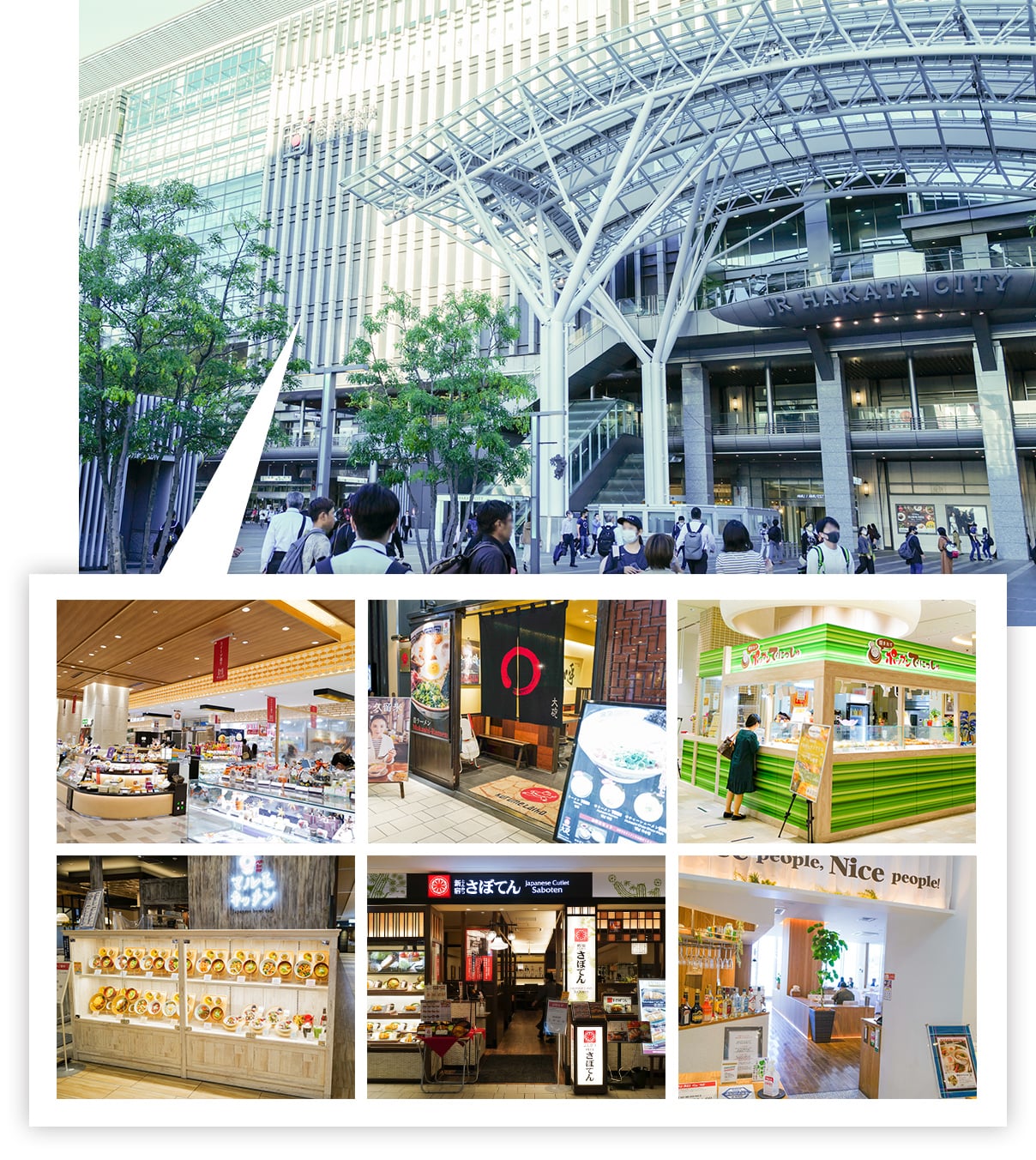
T Hotel
- Rotary Blade Type Bag Breaker & Separator
- Indirectly Heating Type Vertical Dryer
- Food related
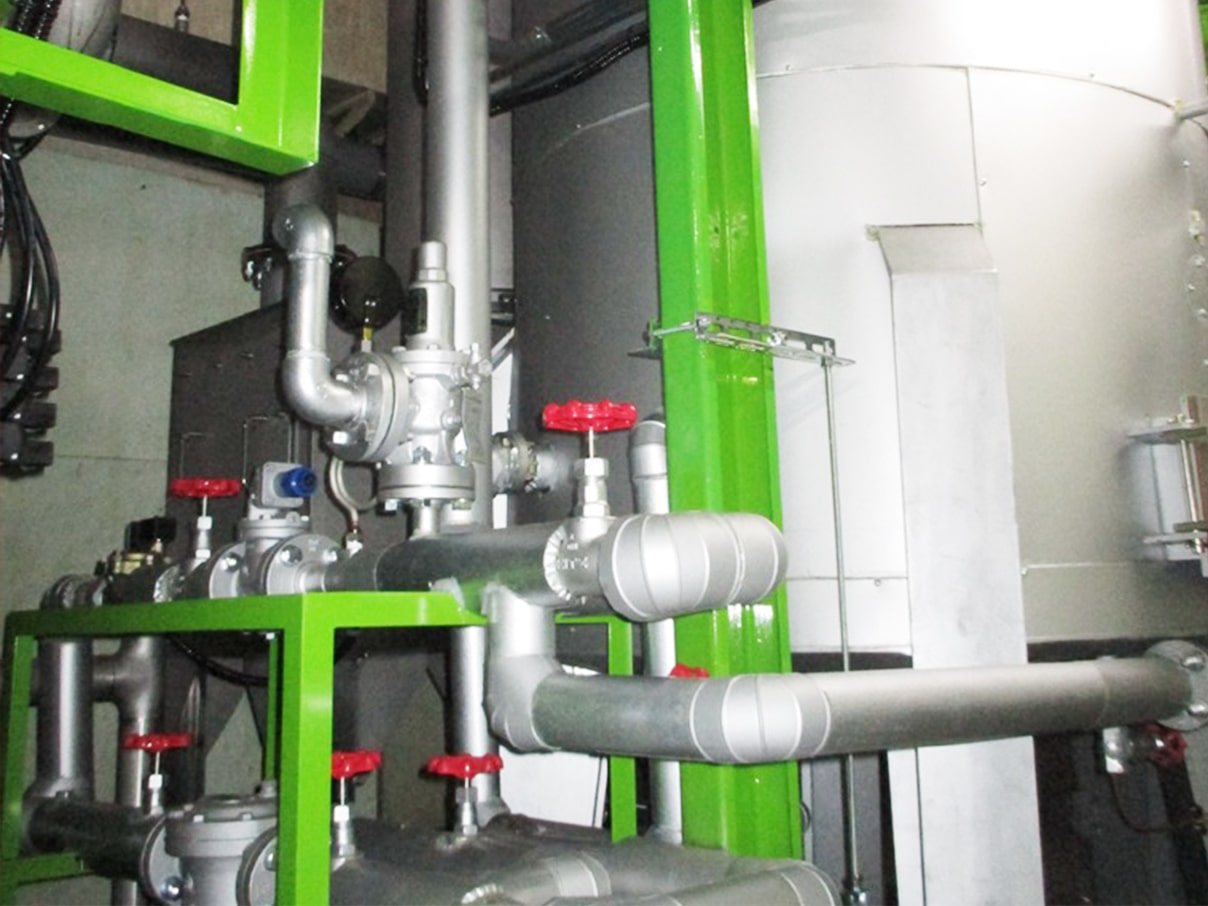
Sanyu’s equipment is also used in some of Japan’s leading luxury hotels in Tokyo.T-Hotel reduces the volume and composts food residue from kitchens and commercial facilities
- Equipment installation area
- Approx. 35m2
- processing material
- Food Waste
- processing volume
- 3,000 kg / day
- Reduction
- The volume is reduced to one-fifth of the amount processed and recycled.
Place of installation
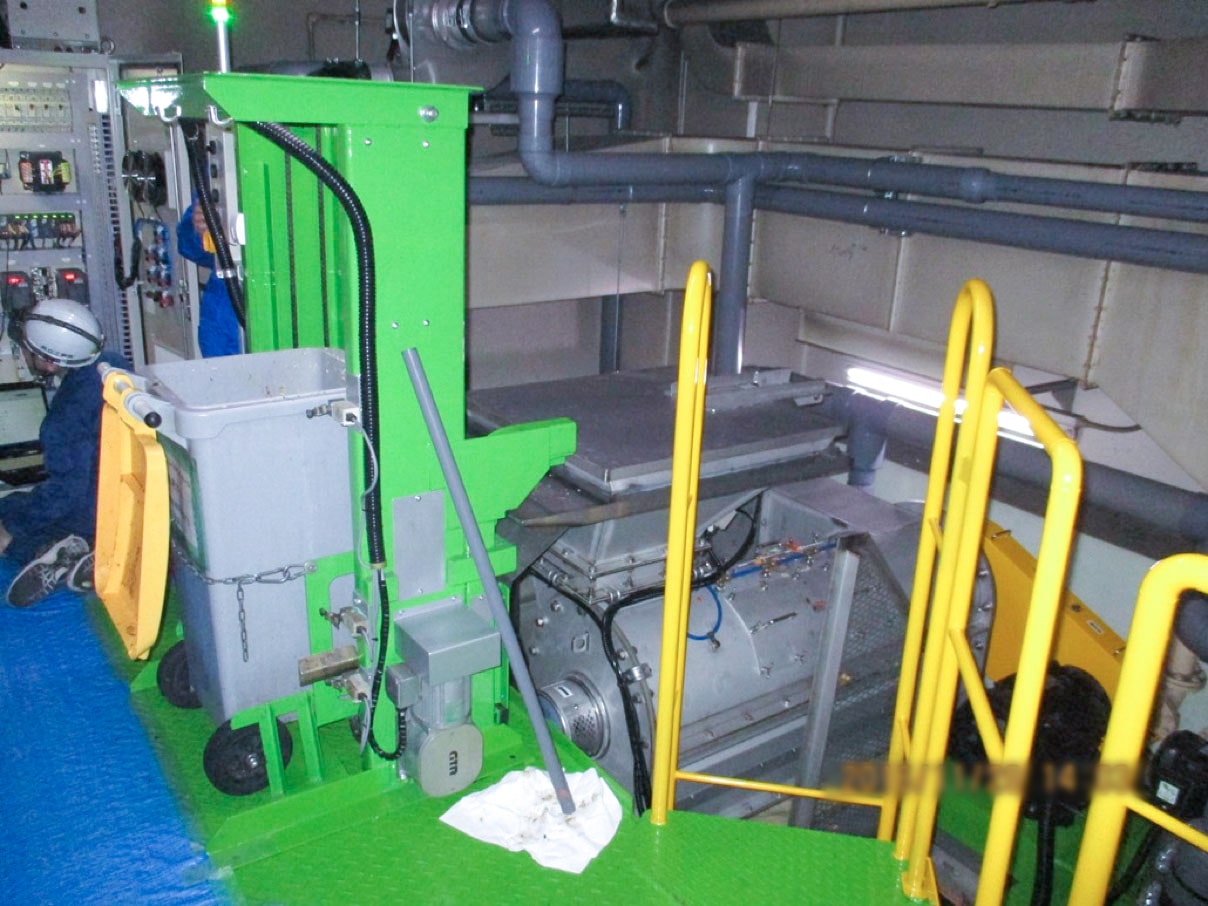
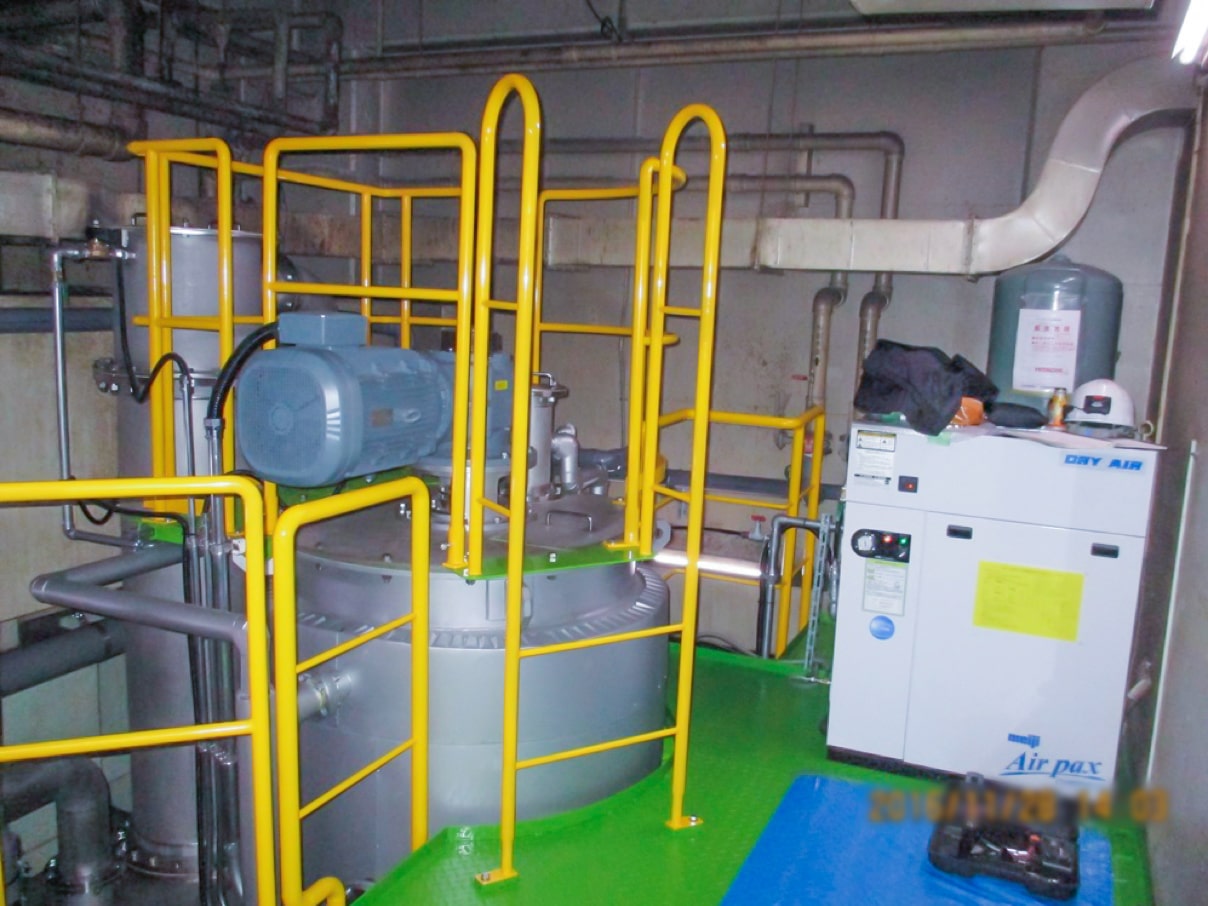
Company A, a food-related company
- Rotary Blade Type Bag Breaker & Separator
- Indirectly Heating Type Vertical Dryer
- Food related
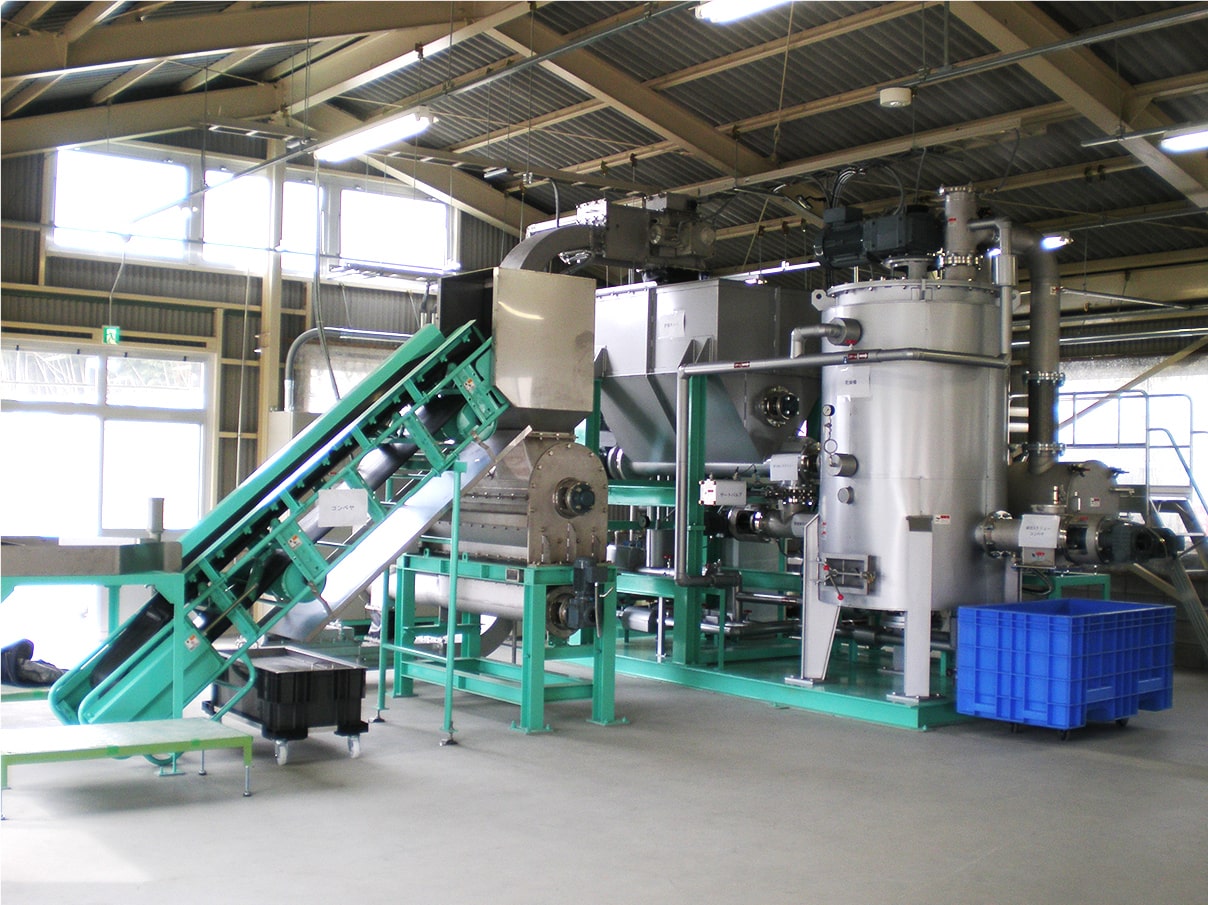
For customers in the city area, we provide equipment and systems that are compact in design and considerate of odor and noise.
- Equipment installation area
- Approx. 90 m2
- processing material
- Animal and vegetable residues
- processing volume
- 6000 kg / day / 24 hours
- Reduction
- The volume is reduced to one-fifth of the amount processed and recycled.
Advantages of equipment installation
Animal and vegetable residues / Content: 80-10% / Processing volume: 1,800 tons / year
Before(USD) | After(USD) | |
---|---|---|
Consignment processing cost | 540,000 | ー |
Running Cost | 74,880 | |
Maintenance cost | 24,000 | |
Disposal cost | 108,000* | |
Labor cost | 60,000 | |
Interest rates | 14,400 | |
540,000 | 281,280 |
* Disposal cost if recycling is not possible
-
Initial cost
(A) 600,000 USD
-
Annual cost reduction
(B) 258,720 USD
-
Equipment depreciation years
(A)/(B) 2.3 years
Benefits for customers who process in house
- In-house processing reduces the cost of disposal.
- Compliance with recycling-related laws (Japan) and ISO 14000
- By making it a valuable material, the issuance of manifests will be eliminated (Japan).
- Improve your image as an environmentally conscious company.
Company B, an Industrial Waste Management Company
- Composting system
- wastes treatment company
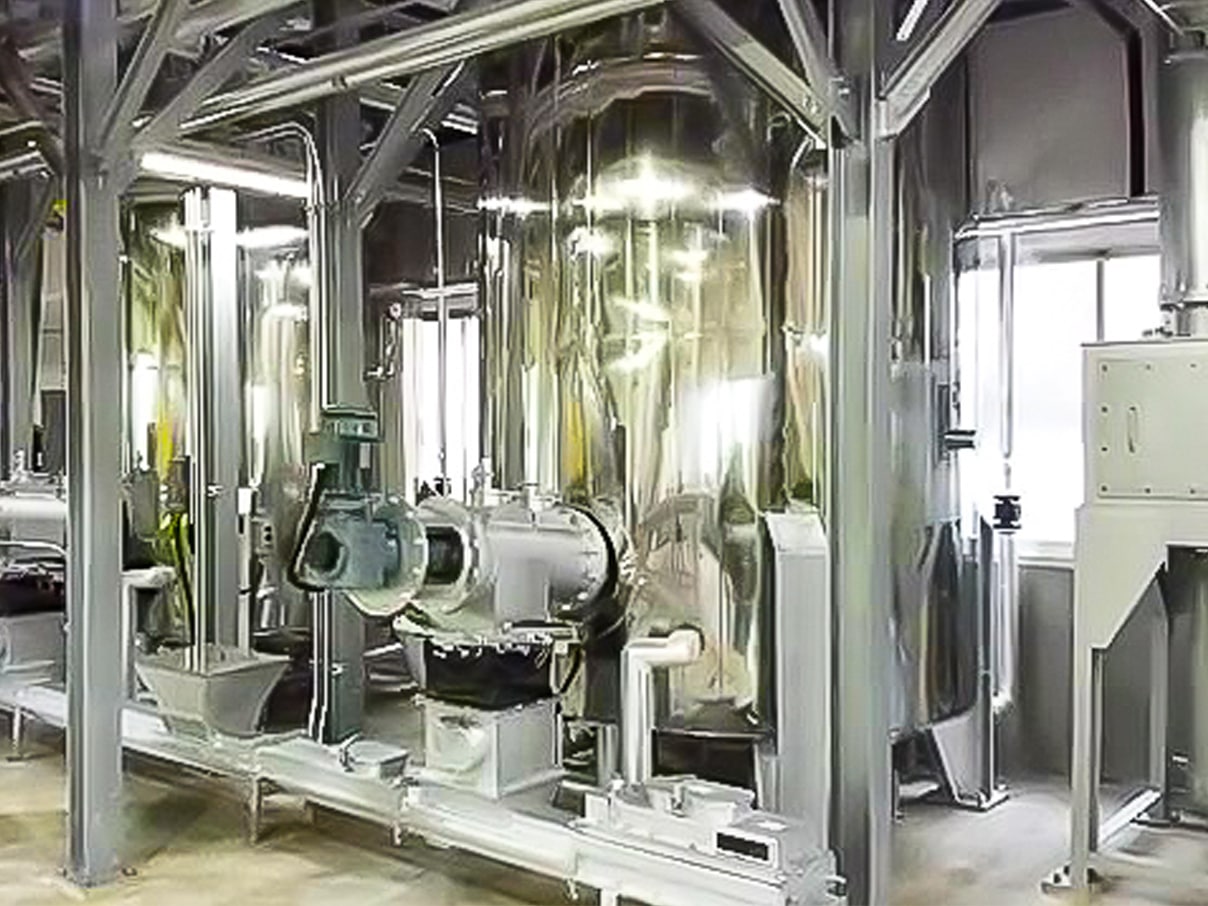
The efficiency of the equipment and system, as well as how it is installed in the limited space, has a great impact on the cost reduction of the business.
In addition, it can be operated 24 hours a day and has excellent durability, which has earned it a high reputation from our customers.
- Equipment installation area
- Approx. 200 m2
- processing material
- Industrial waste (animal residues) generated by food-related companies
- processing volume
- 40 ton / day / 24 hours
Benefits of equipment installation
Animal and vegetable residues / Content: 80-10% / Processing volume: 13,600 tons / year
Before(USD) | After(USD) | |
---|---|---|
Consignment processing cost | 2,040,000 | ー |
Running Cost | 544,000 | |
Maintenance cost | 900,000 | |
Disposal cost | 180,000 * | |
Labor cost | 180,000 | |
Interest rates | 90,000 | |
2,040,000 | 1,084,000 |
* Disposal cost if recycling is not possible
-
Initial cost
(A) 3,000,000 USD
-
Annual cost reduction
(B) 956,000 USD
-
Equipment depreciation years
(A)/(B) 3,2 years
Benefits for contract processors
- Compact design allows for cost savings in equipment costs.
- This system reduces running costs due to its efficient processing method.
- The custom-made system saves space.
- New business opportunities open up as the processed materials can be converted into products, raw materials, and fuel.